The Garage Podcast : S2 EP8
Ray Cornyn of NXP Semiconductors
Ray Cornyn, Senior Vice President and General Manager of Automotive Processors from NXP Semiconductors, talks with host John Heinlein, Ph.D., Chief Marketing Officer from Sonatus about now NXP is working to accelerate software defined vehicles. This episode covers the S32 CoreRide platform, the S32N, the newest and highest performance member of the S32 Vehicle Processor family, optimizing vehicle data…and even Angry Birds.
Listen to audio only version:
Episode Transcript | Ray Cornyn of NXP Semiconductors
Table of Contents
- Overview
- Meet Ray Cornyn
- Fun facts about our guest and John
- Introduction to NXP
- NXP Vehicle Processors
- SDV is more than Angry Birds
- Hundreds of vehicle sensors
- Unlocking the value of vehicle data
- Key automotive industry trends
- NXP S32N Vehicle Processor
- Hardware and IO Isolation
- S32 CoreRide Platform
- Simplifying vehicle validation
- Amplifying corner cases
- Managing EV power consumption
- Conclusion
Overview
JOHN: Today in The Garage, Ray Cornyn from NXP. Let’s go.
JOHN: Welcome to The Garage. I’m John Heinlein, Chief Marketing Officer from Sonatus.
Meet Ray Cornyn
We’re pleased today to welcome a very good friend of ours, Ray Cornyn. Ray is the SVP of Automotive Processors for NXP. Ray, welcome to The Garage.
RAY: Hey, John. Good to be here.
JOHN: So tell us a little bit about you and your background.
RAY: Okay. So I work for NXP and run one of the automotive processor teams there. I’ve got a background originally in engineering, started off in physics. I spent most of my life working in systems and applications. And I’ve ended up running one of the biggest processor teams in the company and in the industry.
JOHN: Yeah. Automotive is a key focus of the podcast. And I know for NXP, it’s an important market. So, we’re thrilled to have you visit with us.
RAY: Okay. Thank you.
Fun facts about our guest and John
JOHN: We always like to get to know our guests at the beginning of the podcast. And so, you’ve got an interesting accent. You got to tell us a fun fact about you.
RAY: Okay. So, I grew up in Scotland, as you’ll tell with the accent. I’ve actually lived in the US for a long time, about 25 years. But one of the problems I’ve always run into in my career is that everybody presumes because I’m Scottish, I’m going to be able to play golf. And so I go and see customers in Japan and Korea, and they always start talking about organizing these golfing events. I cannot hold a golf club. I cannot putt a ball. And so we always get through these embarrassing points where I have to say, no, I’m really sorry, such and such. And then the next question they always ask is, well, I presume you like whiskey. And then I have to admit, really, I drink wine and not whiskey. So I may be pretty good at my job and my engineering background, but as a Scotsman in traditions I’m not particularly great.
JOHN: That’s a good one. Let me see if I can tell you a fun story. I was finishing undergrad. I went to Carnegie Mellon for undergrad. And I… This one professor — when I got into Stanford, I knew I was going to Stanford — I knew this one particular professor was from Stanford. And I said to him, I said, hey, you got to tell me, I’m going to Stanford, what’s your advice? You know, this professor, that whatever. And his advice to me was, “take up golf.” And if you’ve ever been to Stanford, the Stanford University golf course is an unbelievable pro-level course. And as a student, you can play for 16 bucks.
RAY: Oh, not bad at all.
JOHN: And so it… and I did play golf there. I was never amazing. But I did play and it was wonderful. So there’s our fun story for the day.
RAY: So I have the opposite experience. When I grew up in Scotland. First of all, you’ve got to remember what Scottish winter weather is like. And my father played golf throughout the winter. And when I was a child he used to take me along with him. So I was there in the pouring rain and then the wind as my father played golf. And I remember growing up thinking: this is not a sport I want to have anything to do with. So even though now I live in Texas and it’s lovely, I’d never quite get the feeling that that is really what I want to be doing as an exercise or sport.
Introduction to NXP
JOHN: That’s really funny. For our viewers who may be less familiar with NXP, tell us a little bit about NXP, and particularly about your role in automotive.
RAY: So NXP as a company is very well known in Europe, maybe not as much in the US, but we are one of the largest suppliers to the automotive industry. And our history is we’re actually the combination of the original Philips Semiconductor plus Motorola Semiconductor, and both companies had a very large role in automotive through their years of development. And now NXP has a very wide portfolio for automotive solutions. And the area I work in is the automotive microprocessor side of the business. And today in the market, NXP is currently the market leader in the automotive processors and microcontrollers combined.
JOHN: That’s fantastic. And we had Brian Carlson—who I know you work closely with—on the show last year, and we had a wonderful conversation talking about a wide range of topics.
NXP Vehicle Processors
JOHN: I think what I appreciate so much about NXP is the wide range of your processor family, even, in fact, you have multiple families, but even just the family that you manage, which is the S32 family and a few others, there’s so many different levels of that family. Maybe you could give us just a brief overview of that family for a second.
RAY: Yeah. A few years ago, we actually… because of the history of the company and the fact that we’ve come together into NXP, we had a number of different microprocessor type architectures that we had over the years. But about five, seven years ago, we decided that we wanted to go to a unified architecture, which you’ll see is understood as the S32 Architecture. So you’ll see, we did a product announcement called CoreRide. That’s S32 CoreRide. And we decided to make it as simple for both our customers and our tools partners to have a very consistent architecture. And we based those product lines around the Arm architectures, and we use all the different levels of Arm cores to satisfy the different market requirements. But that’s one of the reasons that we’ve had so much success and have been able to satisfy a very wide customer base by having both a wide and deep portfolio for automotive processors.
JOHN: Yeah. Many of our viewers will know that I was at Arm for a long time. That’s where we met at first and started to work together.
RAY: I had forgotten about that.
JOHN: That’s true. That’s true. So I really appreciate the you know… it goes from… sometimes people think software-defined vehicle—and we talk about vehicle software—people sometimes think that’s only IVI, it’s only the screen, or the navigation. But the reality is software pervades the entire vehicle from, yes, the front-facing screen and perhaps the high-performance compute, which we’ll probably talk about today. But also going down into the innards of the sensors and the networking and so on. And you provide software — processors rather — from S32 for all that.
SDV is more than Angry Birds
RAY: Yes, we do. And it’s interesting that, you know, the discussion on software-defined vehicles. I’ve always thought so far in the market, software-defined vehicles, I actually think have been a little bit disappointing. And I think to an extent is that it’s so far it has been very much just the infotainment side. So a lot of people will talk about software-defined vehicles as if it’s really exciting, you’re going to get to play Angry Birds, because you’ll be able to download it onto your infotainment. And that’s not really what the software-defined vehicles is about. It’s the ability to fundamentally change the things that make a car a car, in software. And the reason it’s actually taken a bit longer to happen in the market is the car today is made up of many, many different modules. And they don’t all, openly access all the data that’s in the vehicle. So one of the things that need to happen for software-defined vehicles to really become a reality is you need this change in vehicle architecture. And that’s a lot of the work that we are doing in NXP in our newest processors to allow that access to data throughout the vehicle.
JOHN: Right. We were talking earlier today about data, as you mentioned, and the importance of having access to vehicle data. One of the things that Sonatus does is provide high-resolution data collection and the ability to act on them. So that’s why NXP is such an important partner for us, giving us and giving automakers the chance to really take advantage of data and realize the full promise of software-defined vehicles.
Hundreds of vehicle sensors
RAY: Yeah, yeah, it’s really interesting in terms of if you actually look at the data that is inside the vehicle. Now, today, a lot of that data is, isolated to individual ECUs. And what you see of the future of software-defined vehicles is that effectively, you can access all of the sensors in the vehicle. The thing I’ve always thought amazing is if you look at mobile phones and the applications that now run on those, they have a tiny number of sensors, only 3 or 4 sensors on the phone. If you think all the way those sensors can actually be used together. You know, I don’t think anyone ever thought when they put a flashlight and a camera on a phone, that someone would come up with an idea that you could read blood pressure from that, and that’s the idea — or heart rate from that. And that’s the real idea of doing kind of virtual sensors. Now in a car you have hundreds of sensors. One of the things you realize is you actually have a mobile weather station in your own car. So there’s lots of information and there’s lots of big data analytics that you can do in that information. You know, people get kind of scared by the idea of that. But there’s a lot of, you know, very important, safe data that is in your vehicle that can be used for your benefit and also society’s benefit.
JOHN: That’s right. I mean, you mentioned Angry Birds and I really agree with your approach.
RAY: And by the way I have nothing against that. Angry Birds, it’s a great game. It’s a great game.
JOHN: I like Angry Birds just fine. But the opportunity is much bigger.
RAY: Yes.
Unlocking the value of vehicle data
JOHN: And if you could unlock this data to, for example, do ongoing performance tuning, ongoing efficiency improvements, ongoing safety improvements, then the driver, the vendor, the environment, perhaps, all of these things can get optimized. But today we’re only scratching the surface of what’s possible here.
RAY: And, until we actually get to the stage where the mainstream vehicles have all of the data access and have the analytics, because one of the concerns that’s quite common is if you’ve got hundreds of sensors on each vehicle on the road, and all of them are dumping that amount of data into the cloud, are you really gonna have enough bandwidth to be able to cope with the data and then do the analytics? And one of the important things is actually to make sure you’re sending the right data to the cloud. And that’s where, you know, a lot of the tools, and what we’ve talked about at Sonatus before, is that, you know, how do you actually do that right analysis at the vehicle level so that you’re actually providing, I’ll call it premium valuable data, back up to the cloud.
JOHN: Right. And that’s exactly right. Thank you for saying that. And I think it’s also that the questions you want to ask today, you may not have realized yesterday. Yeah. And it might be different than the question you asked tomorrow as the situation evolves.
RAY: And you’ve got no idea what those questions will be. So I mean, the brute force version of this is you just dump everything that’s in the vehicle. But I don’t know if you can really afford to do that. So what you need is the ability through the lifetime of the vehicle is to decide what data is going to be important to you and be able to choose that. And that will vary throughout the development cycle and the lifetime of the vehicle.
Key automotive industry trends
JOHN: That’s great. It’s a perfect opportunity to shift gears and talk about, you know, you talk to customers all day long. What kind of trends are you seeing and what shifts in the industry are the ones that you think are the most important right now?
RAY: So what you’re seeing at the moment is, you know, historically, the way vehicles were developed and the electronics and vehicles were developed, where every time you added a new function, you effectively added a new box. To the point today that high-end vehicles will have 120 different ECUs. Car companies have started to realize that is not manageable. The development cycles get really long. The data control and the networking has become very, very complicated. So there’s been a move to try and simplify the vehicle architecture, centralizing a lot more of the computing, simplifying the periphery of the vehicle. There’s, you know, some people are taking some really big steps in terms of centralizing a lot of the vehicle functions. And I’m talking here about real-time vehicle functions, not Linux type, you know. And that’s a big difference you have to recognize is that when you’re talking about centralizing functions in a vehicle, you’re talking about centralizing safety and security-critical tasks. So you need very different types of processors to be able to work in that data than what you would normally use for a Linux type / POSIX infotainment kind of applications. And that’s one of the things that’s been driving a lot of the architectural work we’ve been doing inside NXP is how do we allow, you know, previously 40 or 50 functions that were on external ECUs, how can you integrate them actually into a single processor and guarantee in safety and security?
JOHN: Yeah, we were at your launch event — and we’re going to talk about CoreRide in a minute — I was at your launch event in Detroit a few weeks ago. And one of the questions from a really thoughtful journalist said: you know, you’re talking about all of this capability, isn’t this going to increase the cost of the hardware in the vehicle? And the way we answered it, and I really believe this, and I’d love to hear your perspective, is actually while an individual component might be more expensive, in aggregate, in total, actually, because we’re going away from 120 systems to fewer systems in aggregate, we’re going to reduce cost and increase capability at the same time. And I think that’s an important observation.
RAY: Yeah, I think that’s because one of the concerns in the industry has been with all of those additional ECUs that keep getting added, that the cost of the electronic support vehicle has got higher and higher. I agree with you. What you’ll see is more of the value going into the higher performance silicon that’s going to be there in the applications, but you’re going to save a lot in terms of the number of boxes there that you’ve actually got out. And there’s actually a great quote by one of my colleagues, which was, “We are not putting silicon in boxes any longer. We’re taking boxes and putting them into silicon.”
JOHN: I saw that quote and…
RAY: That was a cool quote, actually from Brian, and I thought…
JOHN: I really like that. Our friend Brian we mentioned earlier.
NXP S32N Vehicle Processor
JOHN: Well, this is a perfect segue to talk about S32N because some of what you’re mentioning is, your newest member of the S32 family, the S32N. Which brings some of the ability to have different workloads live side by side and obviously even more types of workloads to live side by side than what was possible before. Do you want to tell us a little bit about that?
RAY: Yeah, we’ve been working on, I would call it, these new kind of hybrid architectures on a couple of our recent generations. And that’s where we’re combining POSIX type functionality along with real-time functionality. But we’ve been very much focused on the ability to isolate functions so that if you take a, you know, a safety critical type application like braking and effectively giving it its own partition in silicon with guaranteed security, guaranteed safety, guaranteed quality of service, and been able to, put many functions together and guarantee that they will not interact with each other in ways you don’t want them to. And we started off with some techniques a couple of years ago. And we’ve really taken those to a new level in the S32N and we first did the first announcement S32N a couple of weeks ago. We did it at Embedded World in Germany, and showed some very, very good demos of how that technology’s intended to work.
JOHN: Yeah. And I think that my understanding is that’s partially by using different Arm processor types, living side by side in the same silicon. So real-time things have a processor that’s suited for their needs versus application type processor things live side by side.
Hardware and IO Isolation
RAY: Yeah, that’s correct. But what we’ve also done is and I’ll call this, our kind of secret sauce is we have a hardware method of isolating the functions in silicon. You know, effectively we can run applications that, you know, if there is a specific hardware I/O and you specifically only want one task to be able to use, maybe some specific safety-critical function, that can actually be enforced in the hardware. So it’s software flexibility by isolation enforced by the hardware. And people have tried doing similar functions using hypervisors and software terms. When people have tried that, it really makes silicon incredibly inefficient. You waste gigahertz of performance trying to do simple tasks. We wanted to make sure that when we built this new architecture that the applications could all run as efficiently on this silicon as they could on their own discrete microcontrollers.
JOHN: That’s critical. Virtualizing I/O has always been a challenge, and it’s done in data centers. But there’s a performance cost. And so as you’re doing that in a real-time system, especially where there’s safety involved, you often can’t afford that. Nor, as you say, do you want to burn all the performance to virtualize. And so what I really appreciate about the.., and I’m a kind of a processor geek. And so I always like to look at the block diagrams. And your processors, especially these vehicle ones, are so interesting because it’s a combination of sort of, if you will, conventional, multicore architecture, plus some very application-specific I/O, application-specific accelerators, and other things married together. I think that’s what’s so interesting about them.
RAY: Yeah. And we’ve spent a lot of time in terms of optimizing certain parts of the IP in the device, especially, as you said, the networking controller that’s in this new generation is a critical part of the functionality of the new product family.
S32 CoreRide Platform
JOHN: So a few weeks ago NXP announced this new platform you mentioned earlier the S32 Core Ride platform. And we were proud to be one of the launch partners for that announcement. I love you to kind of introduce that initiative, what’s the goals, and why did you think it was so important?
RAY: Okay, so one of the principles behind CoreRide and what we’re very much focused on is the auto industry is changing in terms of where the software comes from. Historically, a lot of work was done purely by the tier ones in the industry. And then you’ve seen today, a lot of the OEMs wanted to take on more control and more focus on the software themselves. So we wanted to build a platform that would be very easy to work with the whole ecosystem that is inside the automotive market. So you’ll see that some of the people who are involved with Core Ride are people at Valeo or who are tier one. You’ve seen some other software partners. And then traditional Elektrobit and ETAS. And we didn’t want to be prescriptive. We didn’t want to go to OEMs and say, here’s the only software stack that you can have. You know, if you want to use the N, it has to be X, Y, and Z. So we wanted to…what we’ve always been successful with and proud of is having a wide ecosystem of suppliers. But we recognize now that the OEMs don’t want to spend the time making sure all those pieces work together. They want to know that NXP has worked with the third parties, and all those pieces can come together and they can effectively use it instantly as a platform. So that was really what was behind the principle of CoreRide. It was to make it a flexible platform, but make it a robust and tested-out platform. So, you know, we work with our ecosystem, providers and suppliers to ensure that the tools work together, the software works together. And when it’s effectively handed to an OEM, it’s not just a work in progress, it’s a work that they can start leading their software on top of.
JOHN: That’s right. We were so pleased to be part of that. You know, we’re in production today. You know, in, you know, over a million vehicles and depending on what date you watch this, it may be much, much more than a million vehicles because it’s rapidly increasing. The vast majority of which is based on processors like the S32G that we work in close collaboration with you. So we’re pleased to work on that and be able to take that learning. And we mentioned that, you know, we’ve optimized so much of our software around taking advantage of some of these unique capabilities you baked in, things like network optimization and performance improvements, so that it’s pre-baked in, and customers don’t have to reinvent the wheel.
Simplifying vehicle validation
JOHN: So as you’re talking to customers in all your travels, what feedback are you hearing from customers? What sorts of things are they focusing on with software right now?
RAY: I think it’s dependent on which part of the whole automotive ecosystem you’re talking to. For the car OEMs today, its very much about a wish to control their own software destiny, but also recognizing that they have very, intense time-to-market requirements. So they’re trying to do a balance of what can they develop themselves? But can they do it in a timely manner? They’re all finding the complexity of software and the complexity of integration a real challenge. There’s been a number of vehicles, if you actually look over the last couple of years, where the hardware of the vehicle, the mechanics, the vehicle have all been ready to ship, but the software has not been ready. And it’s such a challenge. Again, one of the things of going to these more of centralized architectures is that that should simplify some of that software and hardware integration, because, as you can imagine, 120 integrated networked ECUs coming together is a really difficult integration task.
JOHN: It is I mean, and it’s a hard computer science problem as well. You think about how do I make sure there’s no deadlock, how do I make sure that there’s no… especially when you talk about real-time and safety aspects. So one of the things we talked about at your recent launch was the increased ability to do things like prototyping in the cloud, the increased ability to do virtual prototyping in simulation, so that in many cases, you can pretest some of these interactions before the hardware even exists, and certainly before the vehicle exists. You mentioned there’s been a number of examples, very noteworthy examples of vehicles being delayed because of some software integration challenge. And when you think about the old way of multiple ECUs that came together relatively late, it’s hard, in some cases, to predict the interactions. And so if you can use some of the mechanisms you’ve talked about, I think we can hopefully pre-vet some of those issues.
RAY: Yeah. And I think that one of the things is really…you know, we talked earlier about the whole principle of software-defined vehicles. And it’s very much been an infotainment thing. And there’s been a number of I’ll call them “own goals” the car industries had in some of those first OTAs in terms of, you know, downloads that haven’t been successful and where the vehicles have ended up actually back at dealers to get those issues resolved. So now when you’re doing that in an infotainment system, okay, the customer is going to get a little bit annoyed. The screen’s going blank, but the car’s drivable. But if you want a proper software-defined vehicle where you can effectively control all of the features in the vehicle, and you’re going to do it through downloads, the testing that you have to do on that before you actually deploy drives a new level of simulation and model virtualization you’re going to have to do in the cloud. There’s some really nice techniques now in terms of effectively building vehicle models in the cloud and then sourcing big data from the fleet. Now, because one of the big problems in automotive has always been you write the software, you write it for 99%, and you’ve been able to test 99% of all conditions. But there’s some corner case that appears there and you never really see the corner case until you have thousands of vehicles driving out in the field. So what you can now do is you build your model in the cloud and you source the data from your fleet. And so you upload it through cloud connectivity. And then you can analyze that data on your new software model they’re about to deploy. So you can now get to the point where you will have spent… you’ll have seen the equivalent of millions of miles on the road of testing before it’s ever been deployed to the vehicle. And that’s, you know, that’s again, stuff that’s getting worked on at the moment. Because I think the last thing anybody wants to see is the car industry moves to software-defined vehicles, and the next thing you get is lots of vehicles stopped in the roads because they’ve been halfway through an update or something like that. So the testing and the thoroughness that’s always been there in the auto industry is guaranteed. It’s, you know, safety and reliability, reputation in this new era. No one wants to take a backward step. Everybody wants it to be better quality, more secure, better safety.
Amplifying corner cases
JOHN: Right. I was just listening to a podcast the other day about exactly this topic, and I think it builds perfectly on what you’re saying, that not only can you do this pre-testing, and not only can you take this, you know, extensive data set before, but you can also artificially amplify the corner cases thousands of times more frequently than they would occur. Like if you… like a right turn. Okay. Well, you know, 90% of the time you drive straight ahead. Well, what if I’m having a problem with right turns? I can just say, give me a million right turns. Well, that would take you normally forever and ever do that. That’s now possible.
RAY: That’s one of the great things you said. And you know when you have models in the cloud, forcing in, you know, normally called fault injection, but if you have that, as you say, you may, you know, it only happens every 14 times I turn left after I’ve turn right three times. Okay. Try and do that in the road. That’s a nightmare. But in the cloud? No problem. You’ll be able to simulate that. So that’s again an area that I think will really see the benefits in the quality for the consumer.
JOHN: Yeah. So that’s an opportunity I would say but then some challenges. You talked about some of the integration challenges. What other challenges do you see that the manufacturers are facing?
Managing EV power consumption
RAY: I think one of the things as you move towards, you know, the electrified future and it’s funny, there’s always discussions about how are EVs growing at the rate they expected. Even if they’re not growing at quite the rate expected, they’re still growing at an incredible rate. But you start to realize that power consumption of the electronics in the vehicle starts to have a big implication on the range of electrified vehicles. So you don’t want to be throwing two kilowatts of processing power at your vehicle, and you want…your networks have to run in a really efficient manner as well. So I think that’s one of the… You know, I did see a comment from a journalist recently and they were trying to hyper-mile their EV. And the funniest thing is I thought: so they did the obvious things, they turned off the AC system, then they turned off the ventilated seats. But the ultimate thing was they turned off the autonomous drive system because they looked at that and realized that that was about a kilowatt of power. And so you realize that all of the modern features and capability we want to bring into vehicles has to be carefully controlled in power consumption, or is just going to be unusable. And so that’s one of the other areas we’re focused on is that, you know, how do you actually add capability and functionality without adding additional power consumption to the vehicle?
JOHN: Well, that’s right. And this is also something you’re known for is power efficient processors because you can just throw extra compute at the problem. You can put a server literally or figuratively in the trunk. But all of a sudden you’ve counter… you’ve got against your own goals of efficiency and range and so on.
RAY: Yeah. There is a story that there was—I wouldn’t I wouldn’t name the company who—but they were doing lots and lots of autonomous drive testing, and they started off in EVs, but they realized they flattened the batteries in the EV so quickly they had to go back and put them into traditional internal combustion engine vehicles, because those were the only ones that could support the computing power of many, many kilowatts in the trunk of the car. So that all has to be thought through and considered.
JOHN: While autonomous driving, which was my previous role in the world, is not our focus of this podcast, it’s not the focus of Sonatus. No one should take from our comments that we’re opposed to that. What we’re really saying is you have to be deliberate and thoughtful about structuring the compute and structuring the vehicle architecture in a way that’s holistic.
RAY: Yeah, it’s holistic. You’ve got to be… energy is energy. You have to work out how you use that most efficiently. And it’s not, as you say, you know, autonomous drive will come in the future. You know, obviously there’s some good inroads already going there, but it’s got to be done in an efficient and costly manner that makes it practical in vehicles. So we can’t go for a green electrified future and then effectively squander all that on heating electronics up.
Conclusion
JOHN: That’s right. It’s a wonderful conversation, Ray. I always enjoy talking with you. I enjoyed seeing you a few weeks ago in Detroit. I look forward to working with you in the future. And we’ll continue to collaborate on CoreRide and other things. And thank you for joining us today.
RAY: Okay. It’s been great to be here. And always nice to talk to the folks from Sonatus. Thank you.
JOHN: Thanks. If you like what you’re seeing on The Garage, we’d love you to like and subscribe to the episode. You can hear about more episodes as soon as they’re published. We hope you enjoy our ongoing conversations on vehicle technology and vehicle software, and we look forward to seeing you again on another episode of The Garage very soon.
Recent episodes
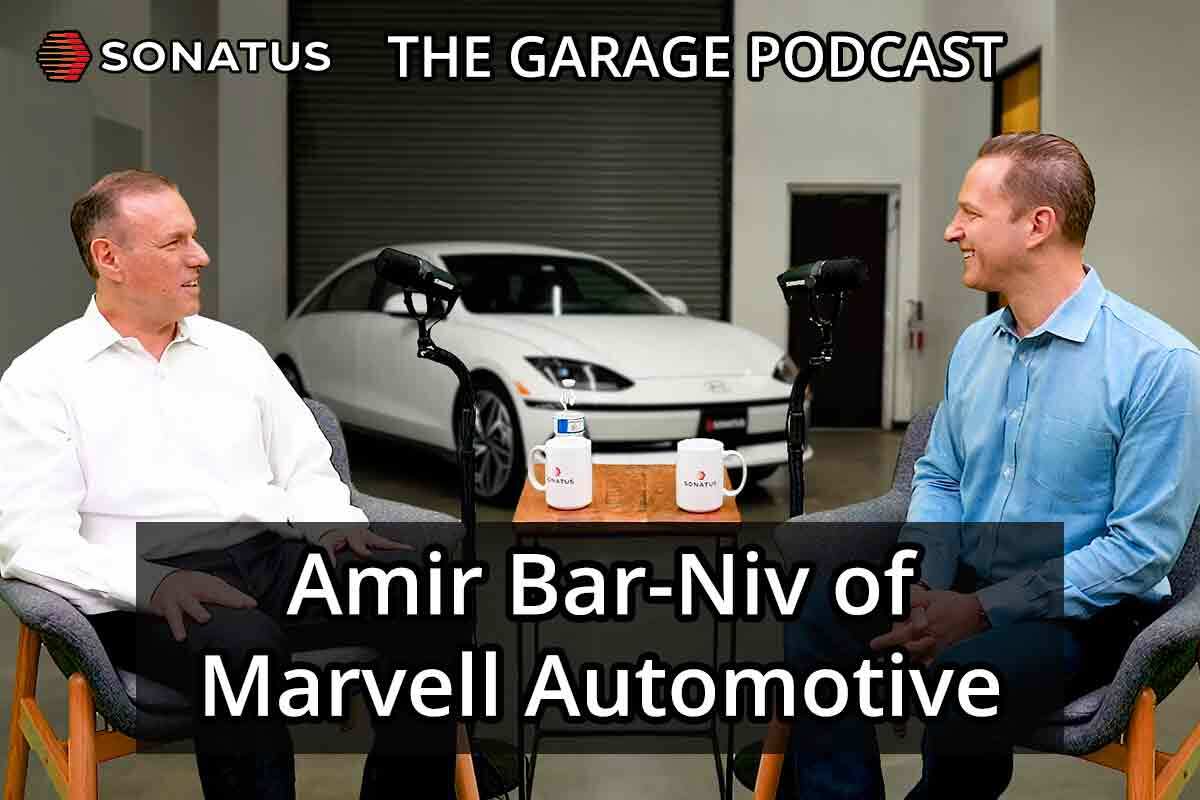
The Garage Podcast
Amir Bar-Niv of Marvell Automotive

The Garage Podcast
Doug Newcomb from AVCC
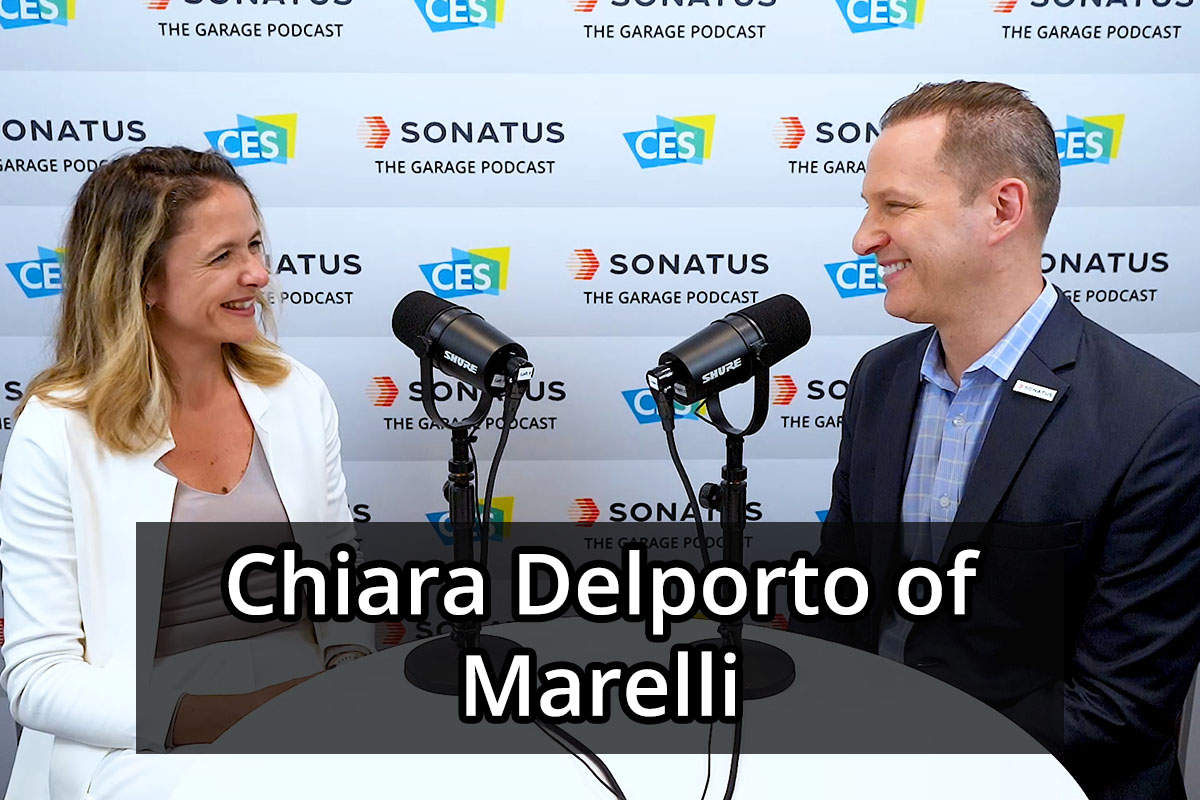
The Garage Podcast
Chiara Delporto of Marelli
Related resources
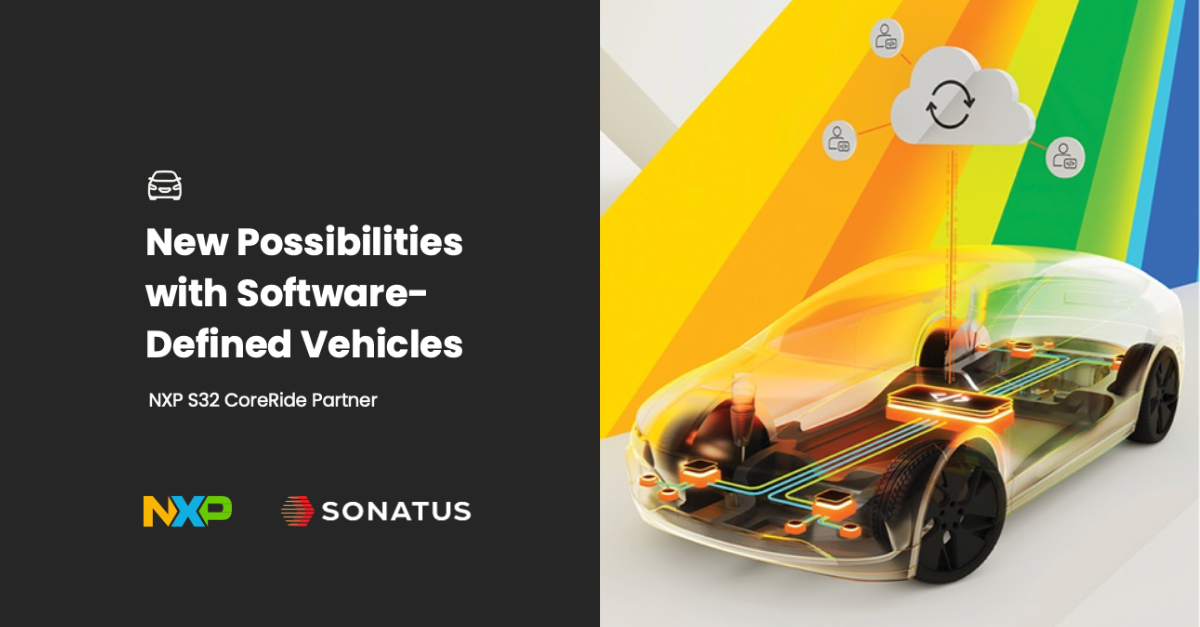
Sonatus Joins NXP’s S32 CoreRide™ Platform
The Open S32 CoreRide™ Platform allows to further streamline the adoption of Sonatus alongside NXP and deliver the next wave of compelling SDVs.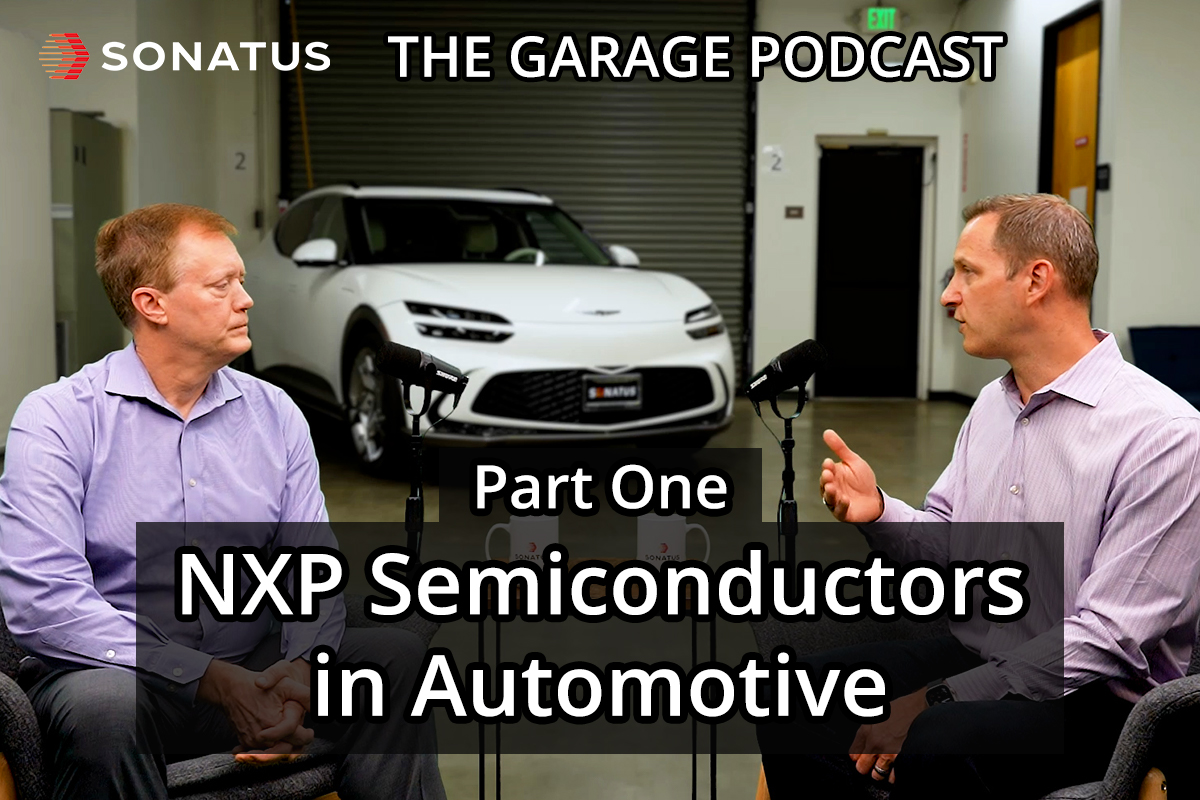
NXP Semiconductors in Automotive, Part 1
In Part 1 of a two-part series, we talk with Brian Carlson, Head of Global Marketing for Automotive Processing at NXP Semiconductors, about the importance of software defined vehicles and the NXP S32 Automotive Platform.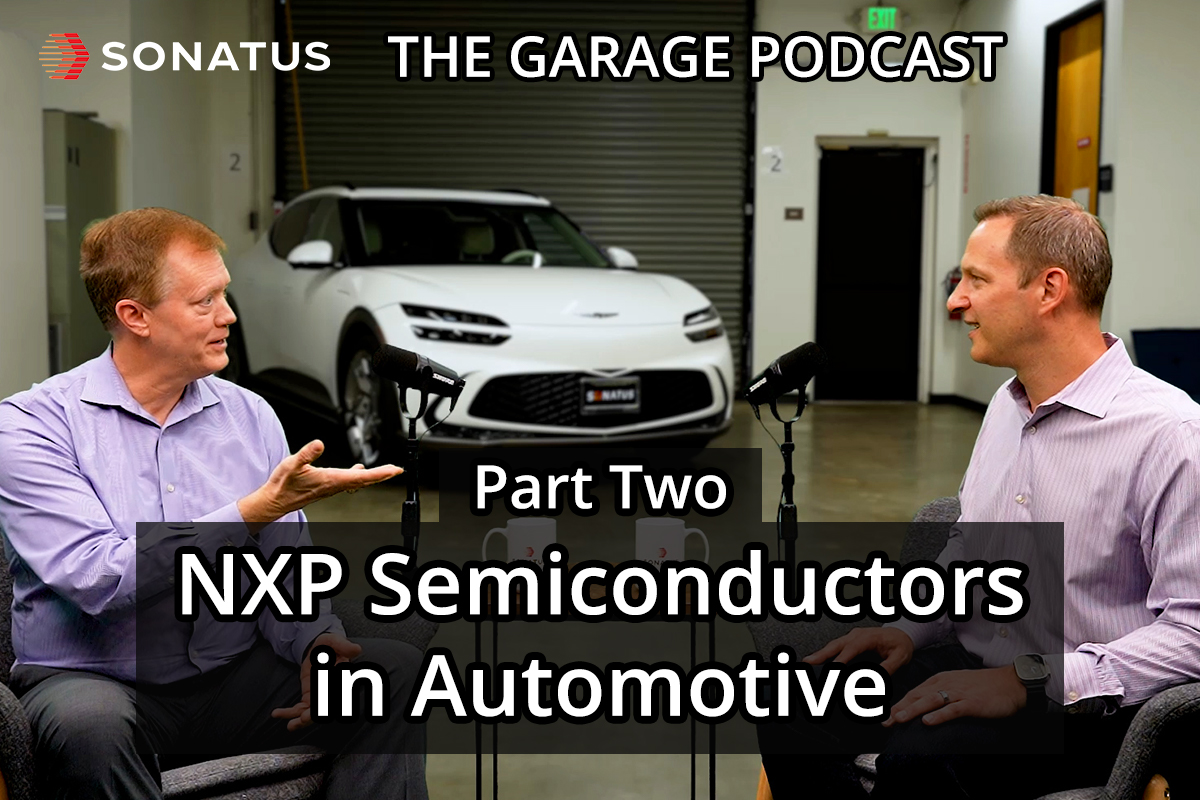